When it comes to choosing between screen printing and digital printing for custom t-shirts, understanding their distinct advantages is essential for making an informed decision. Screen printing offers exceptional durability and vividness, making it perfect for bulk orders with simple designs. Conversely, digital printing provides unparalleled detail and flexibility, ideal for smaller batches or intricate, multi-colored artwork. To determine the most suitable option for your needs, you’ll need to take into account factors such as quality, cost, and production speed. What are the specific scenarios where one method outshines the other? Let’s delve further.
Key Takeaways
- Screen printing is cost-effective for large batches and offers superior durability and vibrant colors.
- Digital printing excels in high-resolution, full-color prints and is ideal for detailed, multi-color designs.
- Digital printing has lower setup costs and is cost-efficient for small runs and customizations.
- Screen printing is versatile across various fabrics, while digital printing works best on 100% cotton.
- Screen printing withstands multiple washes and physical stress, making it more durable for frequent use.
Definition of Screen Printing
Screen printing, a traditional technique in the printing industry, involves the use of a mesh stencil to apply ink onto a substrate, ensuring high durability and vibrant color output. This method, also known as serigraphy or silk screening, employs a squeegee to press ink through the mesh stencil, transferring the design onto the material beneath. The mesh stencil, often made of polyester or stainless steel, is meticulously prepared with a photosensitive emulsion to create the desired image.
In terms of technical advantages, screen printing excels in producing sharp, opaque prints on a variety of substrates, including textiles, ceramics, and plastics. The technique is particularly favorable for large-volume orders due to its cost-effectiveness and efficiency in replicating designs with consistency. Industry professionals appreciate its ability to layer multiple colors with precision, achieving a rich, textured finish that is challenging to replicate with other methods.
Comparatively, screen printing offers superior resistance to fading and wear, making it an excellent choice for items subjected to frequent use or outdoor exposure. This durability is a significant selling point for customers seeking freedom from concerns about the longevity of their custom apparel. By understanding the intricacies of this technique, businesses can make informed decisions about their printing needs.
Definition of Digital Printing
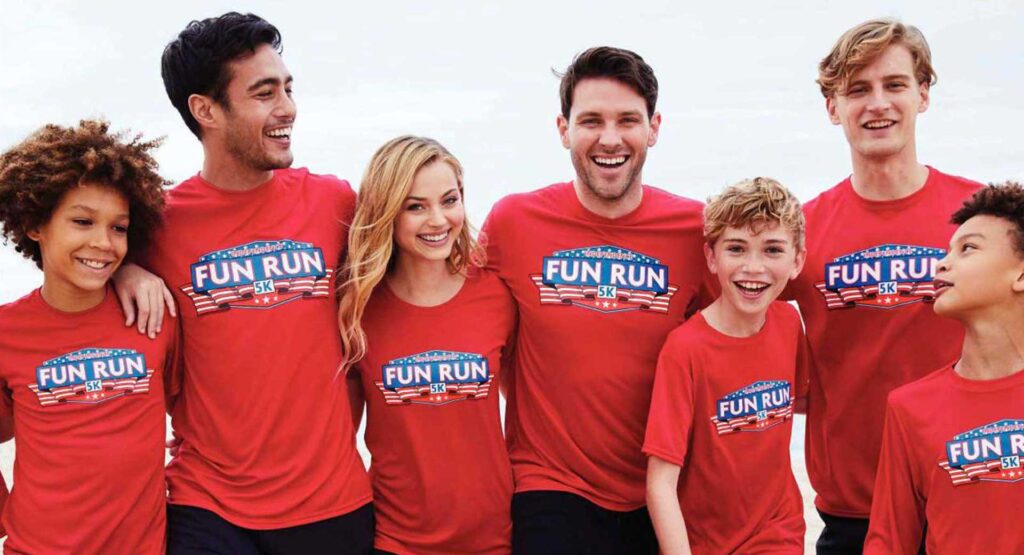
Digital printing, a modern innovation in the printing industry, utilizes digital technology to transfer images directly from a computer onto various substrates without the need for intermediate stencils or screens. This method capitalizes on direct-to-garment (DTG) printers, which apply inkjet technology to deposit water-based inks directly onto the fabric. Unlike traditional screen printing, digital printing allows for a more streamlined process, eliminating the time-consuming setup of creating screens for each color in the design.
One of the significant advantages of digital printing is its ability to produce high-resolution, full-color prints with intricate details and gradients. This is achieved through precise control of ink droplet placement, which can reproduce complex images and photographic quality. Digital printing is highly efficient for small to medium-sized production runs, as it supports on-demand printing and minimizes waste.
In comparative analysis, digital printing offers greater flexibility and customization options, catering to the growing demand for personalized apparel. It also supports a broader color gamut and the use of variable data, allowing for unique prints on each garment. This technology provides unparalleled freedom in design choices, making it an attractive option for those seeking to create distinctive, custom t-shirts.
Quality and Durability
When evaluating the quality and durability of printed garments, it is essential to consider the differences in ink formulation, substrate compatibility, and wear resistance between screen printing and digital printing techniques. These factors significantly impact the final product’s aesthetic appeal and longevity.
Screen printing utilizes thicker ink deposits, resulting in vibrant, long-lasting prints. Its compatibility with a wide range of substrates ensures strong adhesion, making it ideal for heavy-duty wear. In contrast, digital printing uses water-based inks that seamlessly integrate with fabric fibers, offering a softer feel but potentially less durability under extreme conditions.
Key considerations for quality and durability include:
- Ink Penetration: Screen printing achieves deeper ink penetration, enhancing wear resistance. Digital printing, while offering high-resolution images, may result in shallower ink application.
- Color Vibrancy: Screen printing excels in delivering vivid colors due to its thicker ink layers. Digital printing provides a broader color gamut but may fall short in intensity.
- Fabric Compatibility: Screen printing is versatile across various textiles, ensuring consistent quality. Digital printing performs exceptionally well on lighter fabrics.
- Wear and Tear: Screen-printed designs withstand multiple washes and physical stress, whereas digital prints may fade over time, particularly if not properly cured.
Choosing between these techniques hinges on specific project requirements, balancing the trade-offs between visual appeal and enduring wear.
Cost Comparison
A critical aspect to take into account in the cost comparison between screen printing and digital printing is the initial setup expense and per-unit cost efficiency. Screen printing necessitates the creation of screens for each color used in the design, which can be a substantial upfront investment. Conversely, digital printing requires minimal setup, making it an attractive option for smaller orders.
The cost dynamics of each method vary with order size. Screen printing tends to be more cost-effective for large batches due to the spread of setup costs over many units. Digital printing, however, excels in cost efficiency for short runs, given its negligible setup costs.
The following table provides a concise comparison:
Aspect | Screen Printing | Digital Printing |
---|---|---|
Initial Setup Cost | High | Low |
Per-Unit Cost (Small Orders) | High | Moderate |
Per-Unit Cost (Large Orders) | Low | Moderate |
Economies of Scale | Excellent | Limited |
Customization Flexibility | Limited | High |
Given this analysis, businesses should consider their specific needs when choosing between these two methods. For high-volume orders, screen printing offers greater cost efficiency. In contrast, digital printing is advantageous for small, customized batches, providing the flexibility and lower initial costs necessary for short-run projects.
Production Speed
Production speed is a pivotal factor in the printing industry, with screen printing and digital printing exhibiting distinct performance characteristics in this domain. Understanding these differences is essential for businesses aiming to optimize their production workflow and meet market demands efficiently.
High-Volume Efficiency: Screen printing excels in high-volume orders. Once the screens are prepared, the process becomes highly efficient, allowing for the rapid production of hundreds or even thousands of t-shirts. This makes it ideal for bulk orders where uniformity and speed are paramount.
Setup Time: Digital printing, on the other hand, offers significantly reduced setup times. With no need for preparing screens, the process can start almost immediately, making it advantageous for smaller orders or designs that require quick turnaround.
Print Consistency: In digital printing, each print is produced directly from the digital file, ensuring consistent output. However, screen printing can sometimes face variations after extended runs, necessitating occasional adjustments to maintain quality.
- Automation and Scalability: Modern screen printing machines can be highly automated, enhancing throughput. Digital printers, although less scalable for high volumes, provide flexibility and rapid iteration capabilities, essential for dynamic market needs.
Best Use Cases
Identifying the best use cases for screen printing versus digital printing hinges on understanding the unique strengths and limitations of each technology in terms of design complexity, order volume, and material compatibility. Screen printing excels in scenarios where high-volume orders are required due to its cost-effectiveness and efficiency in mass production. It is particularly advantageous for designs that utilize solid colors and minimal gradients. Conversely, digital printing shines in low-volume orders, offering superior detail and color gradients, making it ideal for intricate, multi-colored designs.
Criteria | Screen Printing | Digital Printing |
---|---|---|
Design Complexity | Best for simple, solid-color designs | Ideal for detailed, multi-color art |
Order Volume | Economical for large batches | Cost-effective for small runs |
Material Compatibility | Versatile on various fabrics | Best on 100% cotton |
Material compatibility further differentiates the two methods. Screen printing is versatile, accommodating a range of fabric types, while digital printing is primarily optimized for 100% cotton due to ink absorption characteristics. Hence, the selection should be tailored to the specific requirements of the project, balancing cost, quality, and material considerations. By aligning the printing method with the nuances of the order, one can achieve excellent results that meet both aesthetic and financial objectives.
Frequently Asked Questions
Can I Mix Screen Printing and Digital Printing on the Same T-Shirt?
Combining screen printing and digital printing on the same t-shirt is like merging tradition with innovation. Technically, it is feasible and can yield vibrant, detailed designs. Screen printing excels in durability and solid color areas, while digital printing offers intricate details and color gradients. For those seeking creative freedom, this hybrid approach provides a versatile solution, leveraging the strengths of both printing methods to achieve superior custom apparel.
What Is the Environmental Impact of Screen Printing and Digital Printing?
The environmental impact of screen printing and digital printing varies significantly. Screen printing often uses plastisol inks, which contain PVC and phthalates, contributing to pollution. Additionally, the process generates substantial wastewater. In contrast, digital printing generally employs water-based inks, which are more eco-friendly and produce less waste. However, digital printing’s energy consumption can be higher due to its reliance on advanced technology. Therefore, each method presents unique environmental considerations.
How Do I Care for a T-Shirt Printed Using Either Method?
Caring for a t-shirt printed using either method is like nurturing a delicate flower. For both screen-printed and digitally-printed shirts, turn them inside out before washing in cold water to maintain the print’s vibrancy. Use mild detergent and avoid bleach. Line dry or tumble dry on low heat. While screen prints boast durability, digital prints require gentler handling to prevent fading. This guarantees your custom t-shirt remains pristine and vibrant.
Are There Specific Fabric Types That Work Better With Each Method?
When considering the compatibility of fabric types with printing methods, it is crucial to note that screen printing excels on natural fibers like cotton due to its ink absorption capabilities. Conversely, digital printing is more versatile with synthetic fabrics such as polyester, providing sharper images and finer details. Each method’s efficacy is influenced by the fabric’s fiber composition, affecting durability, vibrancy, and overall print quality.
Can I Achieve Metallic or Special Effects With Digital Printing?
Digital printing can achieve certain special effects, but metallic finishes are challenging. According to industry data, only about 10% of digital printers can produce metallic effects due to limitations in ink technology. While digital printing excels in detailed and full-color designs, screen printing remains superior for achieving high-quality metallic and specialty finishes. For creative freedom and complex designs, digital printing is ideal, though screen printing offers better results for metallic effects.